- In Central Pennsylvania, you can expect to pay around $10 per square foot for a new metal roof, assuming you have a fairly straightforward roof with a few planes and no idiosyncrasies.
- This is a good starting assumption, but metal roofing prices can vary meaningfully based on a variety of factors that we get into below, including your existing roof material, roof pitch, dormers, and more.
Metal roofing is the most durable and reliable modern roofing material in-use today. Rivaled only by copper and slate roofing in terms of lifespan, a properly installed metal roof can last decades with virtually zero maintenance.
Further, metal roofing (and particularly standing seam metal roofing) is a beautiful look, capturing elegance and simplicity in a streamlined profile that can work on both traditional farmhouses and modern, clean-lined homes alike.
For these reasons, metal roofing has become a go-to option for many homeowners: metal roofing cost is usually their first question.
So how much does a new metal roof cost, and is it right for you? Let’s take a look.
Average Cost of Metal Roofing Systems in Pennsylvania
While we’d love to provide a single price-point for every customer, particularly people like you just getting your bearings on the cost of a new metal roof, there’s truly a lot that goes into metal roofing cost.
The best way to price it? Call us for a free consultation on getting a new metal roof in Lancaster County or the surrounding area.
But if you’re not ready for that, here are some guidelines, information on materials, and more.
Metal Roofing Per Square Foot (Average)
$10 per square foot is a good starting assumption for a new standing seam metal roof in Central Pennsylvania.
For an average 1,500 square foot roof, most homeowners can expect a metal roof cost of around $15,000.
Metal roof installation costs are generally 30-40% higher than a traditional shingle roof, including both labor and metal roof materials. A fair assumption for a new asphalt shingle roof in Central Pennsylvania is about $6-7 per square foot.
So what affects that $10/sq. ft. starting point? A lot!
Factors Affecting Metal Roofing Costs (+/- $10/Sq.Ft.)
All of the following factors will affect installation costs for your roof replacement.
But it’s important to note that for a new metal roof, the primary factors that can change are time and labor costs.
All of the following complexities to your roof installation can increase the labor time for the craftspeople at good roofing companies. Let’s take a look. (Then call the roofing pros at Mountaintop Construction for a free on-site consultation).
Number of Roof Planes
The first thing we look for when we see a new roof is how “chopped up” the roof is. A simple saltbox home with two roof angles, each running the entire length of the home, is a much easier and faster project than a 200-year old Victorian home with a variety of roofs and planes. This is generally the biggest factor in sorting out metal roof costs.
Roof Pitch and Angle
These aspects directly influence the ease or difficulty of installation. A roof with a gentle pitch or low angle is typically easier and safer for our team to navigate, whereas steeper roofs demand more precautions. Steeply pitched roofs might require specialized equipment, such as roofing jacks or toe boards, to hold the metal sheets in place before they are secured, and additional safety measures, like harnesses, to protect workers from falls. The steeper the pitch, the more challenging and time-consuming the project can become.
Roof Height
Roof height can sometimes affect installation cost. Higher roofs pose greater risks and often demand more safety equipment or scaffolding setups. This not only increases the time taken for setup and tear-down but also can increase the cost of labor as our team works a little more slowly or relies on lifts more frequently.
Age of the Home
The age of a home can significantly impact the cost of metal roofing installation. Older homes may have structural issues, previous layers of roofing, or outdated construction methods that can present challenges during the installation process. For instance, the roof deck on an old roof might need to be repaired or replaced partially or entirely due to rot. Moreover, older homes often have unique architectural features or intricacies that demand special care, customization, or preservation efforts during the installation. All of these factors can lead to increased labor, materials, and potentially unforeseen expenses during a metal roofing project.
Dormers or Skylights
The presence of dormers or skylights adds complexity to a roofing project. Installing metal roofing around these features requires precision and customization, ensuring there are no leaks or gaps, and it often demands more time for accurate cutting and fitting. Consequently, the presence of such architectural elements can significantly drive up the cost of a metal roof installation.
Flashing Requirements
Metal roofing that butts up against brick or stone walls, as good examples, require counter flashing, which provides the waterproof seal between the stone wall and the metal roof panel’s edge. This is the case with most roof to wall material, and it requires some expertise and additional time to waterproof properly.
Trim Details
Complex valleys, edges, and capping require meticulous attention to detail and often need custom-cut pieces or specialized trim to ensure a seamless and watertight finish. These intricate trim details not only enhance the aesthetic appeal of a metal roof but also ensure its longevity and functionality. As these details demand additional labor, they can increase the overall cost of the roofing project.
Existing Roof Materials for Removal
The type and condition of existing roofing materials that need to be removed before the installation of metal roofing can substantially influence the cost and duration of the project. For instance, asphalt shingles, which are relatively light and easy to detach, might be less labor-intensive to remove compared to clay tiles, wood shakes, or (worst) multi-layered roofing. Removing several layers is more time-consuming and requires disposal of a larger volume of waste, leading to higher costs.
Our ultimate goal is to build beautiful, weatherproof metal roofs with precise angles and joints that look great! All of the above can affect how easily and quickly we can do our job to the best of our ability!
A Metal Roof’s Cost Over Its Lifetime Compared to Shingles
As you consider which roofing material is right for you, it’s important to take into account not just up-front costs, but lifetime costs for your roof replacement.
A metal roof will last 60 years or more, and many metal roof paints are guaranteed by the manufacturer for at least 35-40 years. That warranty usually applies to the paint on both corrugated metal panels and standing seam panels alike, and the underlying metal can last far longer if properly cared for.
This means that with paint re-application, a properly installed metal roof can last another few decades or more! We’ve seen metal roofs that are over 100 years old, though they can require a little more maintenance as they age.
All of this means that a metal roof can last 2-4x as long as an asphalt shingle roof. Let’s look at a realistic comparison of shingles versus metal over the course of 50 years. We’ll use a 1500 square foot average roof size for our analysis.
New Metal Roof Cost Over 50 Years
Initial installation: $15,000
Re-painting and replace degrading fasteners at year 50: $3,000
Total Cost: $18,000
New Asphalt Shingle Cost Over 50 Years
Initial installation: $10,500
Replacement at year 25: $10,500
Replacement at year 50: $10,500
Total Cost: $31,500
Even if you assume you only live in the house for 25 years as you approach retirement, the cost-savings from a metal roof still outperform asphalt shingles. And, this analysis assumes no repairs to the asphalt shingles periodically, which is common after severe weather events with asphalt shingles. Steel roofs or aluminum roofs simply don’t have the same issues with shingles blowing off.
And, this analysis fails to account for the beauty, curb appeal, and potential retained property value for homeowners re-selling a home with a metal roof!
Benefits of a Metal Roof
Chances are you’re here because you recognize the benefits of a metal roof over asphalt shingles, but it’s worth touching on the highlights. Overall, a metal roof will last longer, provide greater efficiency in the home, and can even improve the resale of your home in the future.
Metal Roof’s Longevity
Metal roofs can last 50-100 years depending on material and installation techniques. In contrast, traditional asphalt roofing materials have an estimated lifespan of 20-30 years. Thanks to hidden fasteners that are not exposed to the elements, standing seam metal roofs can last 100 years or more!
Metal Roof’s Durability
Metal roofs can withstand extreme weather conditions, including high winds, heavy snow, hail, and even wildfires. Properly installed metal roofs rarely suffer leaks or loose panels, both problems that can crop up with asphalt shingles given the number of “seams” and nails involved.
Metal Roofing Material is Environmentally Friendly
Metal roofs are often made from recycled materials and are 100% recyclable at the end of their lifespan. Asphalt shingles contribute to millions of tons of landfill waste annually.
Energy Efficiency From Metal Roofing
Metal roofs reflect solar radiant heat, reducing cooling costs in the summer by as much as 10-20%!
Metal Roofing Materials are Low Maintenance
Most metal roof materials require minimal maintenance, reducing long-term upkeep costs. They don’t rot, warp, split, or crack.
Resale Value with a Metal Roof
Homes with metal roofs often see a small increase in resale value due to the longevity and lower maintenance of the roofing system, particularly for discerning homebuyers who know what they’re looking for. Like a swimming pool, they can attract a very specific buyer.
Weight of Metal
Metal roof material is lightweight, putting less stress on a home’s structural support compared to heavier asphalt shingles, tile, or slate.
Snow Shedding
The slick surface and the design of metal roofs allow snow to slide off easily, reducing the risk of ice dams or heavy snow buildup that can affect the underlying structure over time.
Metal Roofing Materials: Standing Seam Versus Corrugated Explained
Metal roofing comes in two primary profiles: standing seam and corrugated, sometimes called an “ag” panel or “3-rib” metal roof type.
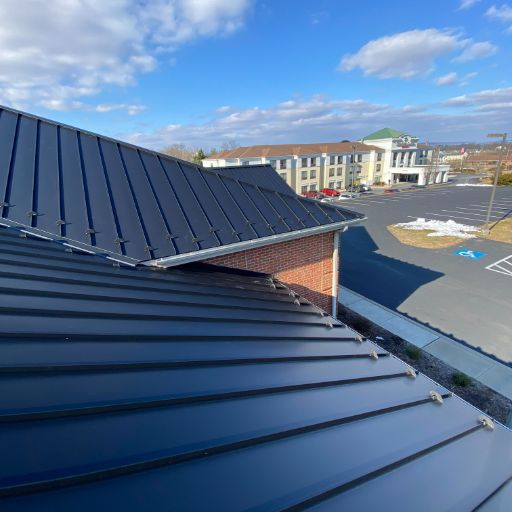
Standing seam systems provide an elegant, functional metal roof. You’ll be familiar with these panels thanks to a single 1- or 2-inch high “seam” that serves to connect each panel as it runs vertically along your roof plane. This seam is apparent every 16-20”, depending on the panel width. The benefit of standing seam is that there are no exposed screws or nails, and these are entirely concealed fastener panels. This is not only a compelling aesthetic, it also means there are no exposed fastener heads that can lead to roof leaks. For this reason, standing seam panels can last for generations.
Traditional corrugated or exposed fastener panels are also a great, durable material. The roofing screw that holds these panels in place includes a rubber washer to seal the point of penetration. While this is a highly efficient way to secure panels, over time that rubber washer can wear down, typically over the course of 10-20 years, and some may need to be replaced to avoid a roof leak.
Exposed fastener panels are often slightly cheaper than standing seam due to the higher labor costs involved in properly installing concealed fasteners.
Metal Roof Material Options
With a new metal roof, you also have some material options among metal panels.
Steel
Most metal roofing you see today is painted steel. A steel roof is tried-and-true, usually carries a 35-40-year warranty on the paint, and is the go-to for a good roofing contractor.
Galvanized Steel
Through the galvanization process, galvanized steel has been treated for corrosion and rust resistance and does not require paint. If bare metal is the look you’re after, galvanized steel is an alternative to painted steel.
Aluminum
Aluminum will theoretically never rust, which is why it it is more expensive than both galvanized and painted steel. It is available in a variety of colors.
Copper
Copper roofs are a decadent look, but that incredible curb appeal comes at a cost. Like aluminum, it will never rust, though it will “patina” and turn a historical green color over time as it oxidizes. Some homeowners opt for copper metal trim or copper metal gutters as a cool accent instead of their whole roof.
Zinc
Zinc is another highly durable and beautiful material, though it will dramatically drive up roof cost. Zinc roofs are not common today.
Tin
Tin roofs were common in the roofing industry 75 years ago, particularly on barns, but today have been largely replaced by steel and aluminum. Today, few manufacturers will even make a tin roof.
Frequently Asked Questions About Metal Roofing and Metal Roof Costs
How long does a metal roofing installation take?
Most of our metal roofing projects take one to two weeks to complete.
Is it cheaper to get a metal roof or asphalt shingles?
Most metal roofs will cost less than shingles over the course or their lifetime. While upfront costs tend to be a little higher, this is largely due to increased material costs: an experienced roofing contractor will spend alil more TIME installing a metal roof, meaning labor costs are lower, though material costs make up the difference.
Do most roofers install metal roofs?
Not all roofing companies install metal roofs, and it’s a good idea to consider a roofing company that specializes in metal roofing. Metal roofing materials carry their own challenges, and while it often seems that everyone and their brother has a shingle roofing company, installing metal panels properly does require some attention to detail.
Can I put solar panels on a metal roof?
Absolutely, and most metal roofs will work really well with solar panels! In fact, you can install solar panels onto a standing seam metal roof without even penetrating the metal roofing material! In this case, small clamps can be applied to the heightened seam, with no screws or holes necessary in the material.
What’s the most expensive metal roofing material?
When it comes to a metal roof cost, copper and zinc are the most luxurious and pricey products you can find.
Schedule A Free Consultation And Unlock the Lasting Strength of Metal Roofing with Mountaintop Construction
Ready for your own free metal roof quote?
Elevate your home’s protection, efficiency, and value. Reach for the pinnacle of roofing solutions with Mountaintop Construction today!